Scania 社が、受賞に輝いた長距離トラック向け低燃費ドライバー支援システムを開発
「Simulink は開発プロセスの 2 つの段階において特に役に立ちました。まず開発初期には、Simulink を活用してアイデアを試作し、どのように機能するかを可視化することができました。そして、コードを生成して車内テストを実施した後には、何回かのシミュレーションを行い、設計を調整して、次の繰り返しのためのコードを生成することができました。」
課題
運転技術に関するフィードバックをトラックのドライバーに即時に提供する、リアルタイムのドライバー分析システムを開発すること
ソリューション
ドライバー支援システムの設計とシミュレーション、 プロトタイプと生産ターゲットの組込みコードの生成、ユーザー インターフェイスのプロトタイプの構築に、MathWorks のモデルベース デザイン ツールを使用
結果
- 開発期間の短縮および手間の削減
- モデルのカバレッジの向上
- 回帰テスト時間の削減
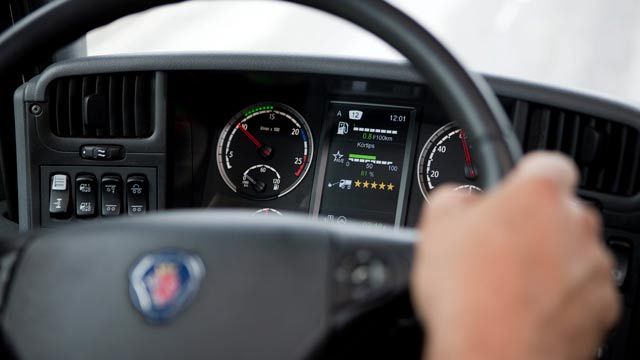
Scania ドライバー支援表示パネル
ドライバーの運転技術が未熟な場合、二酸化炭素排出量や燃料消費量は最大10%増加します。たとえば、ある会社が 20 台のトラックを所有し、各トラックが毎年 120,000 キロ (75,000 マイル) 走行した場合、二酸化炭素排出量が 200 トン、そしてコストが 66,000 ユーロ増加することになります。
Scania のドライバー支援システムでは、ダッシュボードのコンソールから、ドライバーへ即時にフィードバックが提供されます。同システムによる運転技術の向上は、燃料消費量の削減、安全運転、ブレーキおよびその他部品の劣化・損傷の軽減につながっています。現在 Scania のR シリーズ トラックに搭載されているこのドライバー支援システムは、MathWorks のモデルベースデザイン ツールを使用して開発されました。
Scania の主任エンジニアである Jonny Andersson 氏は次のように述べています。「システムを Simulink でモデリングすることで、開発の早期段階で、アーキテクチャの定義、ならびに設計の可視化が可能になり、 さらに設計のデバッグを行うためににシミュレーションを実行することができました。 また、Embedded Coder では、早期のリアルタイム プロトタイプと量産システムの両方のコード生成を行いました。この結果、低レベルのコードを使用するのではなく、モデルで設計を調整することができました」
課題
コストを低く抑えるために、Scania では車両にすでに搭載されているセンサーから入力を得て、運転のシナリオを解析したいと考えました。このため、いくつかの鍵となるメトリクスを数学的に導き出す必要がありました。システムでは、ほとんどの場合 CAN バスを通じて、個々の車輪の速度、エンジンのトルク、エンジン速度、車両速度、使用中のギアといった、100 以上の入力にアクセスできました。このプロジェクトでは、これらの入力をドライバーの運転パフォーマンス評価に変換するアルゴリズムの開発が主な課題となりました。
また Scania では、開発期間を短縮し、実際の ECU で早期に設計の検証を行いたいと考えていました。さらに、さまざまなドライバー表示パネル設計を開発および評価する必要がありました。
Scania は、エンジニアが開発早期にアイデアを試作でき、さらにシミュレーションとコード生成によって実施テストとプロトタイプの数を削減できるシミュレーション環境を必要としていました。
ソリューション
Scania では MathWorks のモデルベースデザイン ツールを使用して、ドライバー支援システムのモデリングとシミュレーション、ユーザー インターフェイスのプロトタイプ開発、プロトタイプおよび生産ターゲットのための組込みコードの生成を行いました。
設計は、ドライバーの坂道での運転、ブレーキの使用、ギアの選択、予測を評価するために、サブシステムに分割されました。次にこれらのサブシステムが、ディスプレイを制御するコンポーネントとともに、Simulink® でモデリングされました。また、Stateflow® を使用して、ドライバーに更新情報を提供するために、どのような状態での運転が安全かを判定する制御ロジックがモデリングされました。Scania のエンジニアは実施テストを行って、CAN バスからさまざまな地形や交通状況でのトラック センサー データを収集し、このセンサー データを入力として Simulink でシステムのシミュレーションを行いました。また、障害が発生した状況や、実際の運転テストでは再現が困難または不可能なその他の状況についてもシミュレーションが行われました。
一方、MATLAB® を使用して、Scania ドライバー支援システムの出力を表示するユー ザー インターフェイスのプロトタイプが開発されました。次に MATLAB Compiler™ で、トラックで使用されていたインターフェイスのスタンドアロンの実行可能ファイルが作成されました。
さらに Embedded Coder® でコードが生成され、プロトタイプの ECU に実装されて、リアルタイムの実施テストが可能になりました。
この開発期間全体を通じて、モデルが Scania のモデリング基準を確実に満たすように、Simulink ではモデル アドバイザー ツールが利用されました。これらの基準は、Simulink を利用した同様のプロジェクトから学んだ教訓と、MAAB ガイドラインに基づくものです。これらの多くは簡単に遵守できるように、 モデル アドバイザーにカスタム チェックとして取り入れられています。
また、シミュレーション中には Simulink Coverage™ を利用してモデルのカバレッジが解析され、設計内でテストが実施されていない要素が特定されました。
シミュレーションと実施テストでシステムを徹底的にテストした後に、Embedded Coder でターゲット ECU の量産コードが生成されました。この ECU は現在、Scania の R シリーズ トラックに搭載されています。初期のテストでは、このシス
結果
- 開発期間の短縮および手間の削減. Andersson 氏は次のように述べています。「MathWorks ツールを使用することにより、手作業でコーディングを行った場合と比較して、少なくとも 6 か月早くプロジェクトを完了することができました。MathWorks ツールがなければ、このプロジェクトにはエンジニアがもう 1 名必要でしたが、その代わりに、Simulink と Embedded Coder のおかげで、より高いレベルでアルゴリズムの設計作業に専念することができました」
- モデルのカバレッジの向上. Simulink Coverage を利用することで、Scania はテスト中に状態カバレッジと判定カバレッジの解析を行い、95% 以上のモデル カバレッジを達成しました。
- 回帰テスト時間の削減. Simulink によって、回帰テストに必要な時間が、実車による 3 時間からシミュレーションでの 20 分に削減されました。また、これらのテストは、他の多くのテストとともに夜通しで実行できました。