東風電動車両、モデルベースデザインを使用してハイブリッド電気自動車のバッテリ管理システムを開発
「モデルベースデザインの導入により、アイデアの発案から量産コードの生成に至るまでの開発プロセスを統合することができました。 MathWorks ツールのおかげで、設計の早期段階から連続的な検証が可能となり、我々が持つ高度な技術力を活かして重要なバッテリ 管理技術の開発ができるようになりました」
課題
ハイブリッド電気バス用のバッテリ管理制御システムを開発すること
ソリューション
コントローラー設計のコードをモデルリング、検証、生成するために、MathWorks のモデルベースデザイン ツールを採用
結果
- 予定より早くプロジェクトを完了
- 設計の再利用が可能に
- すべてのアプリケーション コードを自動生成
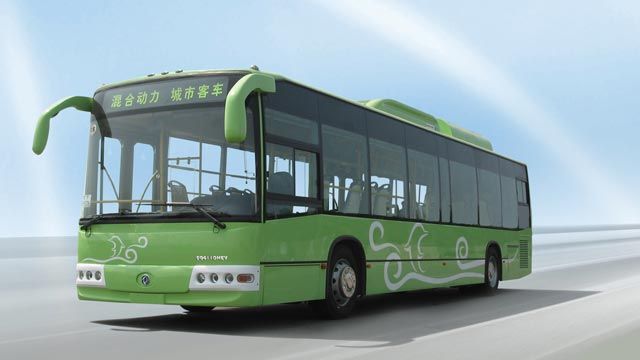
東風 EQ6110 ハイブリッド電気路線バス
東風電動車両は、中国の東風汽車有限公司の研究開発部門で、電気自動車やハイブリッド電気自動車の研究開発を行っています。同社ではトラクション モーターやバッテリなどのほとんどのコンポーネントをサプライヤーから調達しています。しかし、バッテリ管理と車両エネルギー管理の制御方法は、ハイブリッド電気自動車の性能と燃費にとって非常に重要であるため、また、これらのコントローラーは車両レベルで最適化および統合する必要があるため、東風電動車両ではハイブリッド電気自動車の電子制御システムを、同社独自の知的財産の一部として、社内で開発することに決定しました。
東風では MathWorks のモデルベースデザイン (モデルベース開発、MBD) ツールを利用して、同社のハイブリッド路線バスである EQ6110 のために高度なバッテリ管理制御システムを開発しました。このバッテリ管理制御システムは、標準的な路線バスに比べ、燃費効率を 30% 向上させると同時に排気ガス削減にも貢献します。
東風電動車両の主任技術者、Xiaokang Liu 博士は次のように述べています。「このコントローラー モデルの開発と量産コードの生成はわずか 6 名のエンジニアで行いましたが、すべての作業を目標期限内に、予算内で完了しました。また、連続的に検証を行い、閉ループ シミュレーションにプラント モデルを使用することで、早期の段階に問題を特定して解決でき、当社の高い品質水準を上回ることができました」
課題
東風のエンジニアは C 言語でコントローラーを開発した経験はありましたが、今回のバッテリ管理システムのプロジェクトはこれよりかなり複雑でした。また、車両の制御システムの統合も課題でした。
Liu 博士は次のように述べています。「複数の専門分野にまたがるプロジェクトでは、開発スタイルが非常に異なるため、C 言語に基づく実装においてデバッグと保守管理が困難になります。当社では人的資源や物的資源が限られているので、18 か月という厳しいスケジュールを考えると、手作業によるコード作成は現実的ではありませんでした」
また、東風のエンジニアは ISO/TS 16949 の品質管理ガイドラインに準拠しなければならず、作成するコードは、東風が遵守する MISRA ® C の品質規格に適合しなければなりません。「連続的な検証を可能にし、矛盾のない、基準に準拠した、効率的な量産コードを生成する開発環境が必要とされました」
ソリューション
東風電動車両のエンジニアは MathWorks ツールとモデルベースデザインを利用して、まずバッテリ管理制御システムの設計、シミュレーション、検証を行い、その後量産コードを生成しました。
まず、決定されたプロジェクトの要求仕様に基づき、MATLAB®、Simulink®、Stateflow® を活用してコントローラー モデルの最初のバージョンが浮動小数点で開発されました。これと並行して、テスト データを使用してバッテリの Simulink モデルが開発されました。このモデルは、コントローラー モデルとともに使用され、コントローラーの設計を検証するために必要なバッテリ ダイナミクスに関する情報を提供しました。
単体テストを行った後、Simulink でコントローラー モデルがバッテリ モデルにリンクされ、デスクトップ シミュレーションを実行してアルゴリズムの基本的な機能が検証されました。
また、コントローラーのアルゴリズムを微調整するために、Simulink Coder™ を使用して短時間でモデルからコードが生成され、このコードがラピッド プロトタイピング コントローラーで実際のバッテリに対して実行されました。
次に、Fixed-Point Designer™ を使用してモデルが浮動小数点から固定小数点に変換され、2 回目のデスクトップ シミュレーションを行って変換が適切に行われたことが検証されました。ここでは変更条件判定カバレッジ (MC/DC) のメトリクスが収集され、テストの完全性が評価されました。
さらに、Embedded Coder® を使用して、モデルから量産コードが生成されました。次に SIL テストが行われ、閉ループ シミュレーションで Simulink バッテリ モデルに対してコードを実行し、生成されたコードが予想通りに動作することが検証されました。
検証の最後の段階では、Freescale™ S12 マイクロコントローラーに基いて、ターゲット ECU にコードが実装されました。また、プラント モデルから生成したコードを使用して、HIL シミュレーションで ECU が実行され、コントローラー ソフトウェアと ECU ハードウェア間の統合が検証されました。
その後コントローラーは、実際の走行での信頼性と耐久性をテストするためにプロトタイプ車両に搭載され、量産コードとともに生成された ASAP2 キャリブレーション ファイルを利用して CANape でキャリブレーションされました。
この組込みバッテリ制御システムは、現在試験走行中の東風汽車有限公司の EQ6110 バスに実装されて�
結果
- 予定より早くプロジェクトを完了. Liu 博士は次のように述べています。「最初のアイデアからコンセプト実証、製品の完成まで、わずか 18 か月しかありませんでした。しかし、モデルベースデザインを活用し、コードを自動生成し、浮動小数点から固定小数点への変換を効率化することで、わずか 6 名の技術者チームでプロジェクトを予定より早く終わらせることができました」
- 設計の再利用が可能に. 東風電動車両では、現在開発中のセダン型ハイブリッド電気自動車にもこのコントローラー設計の一部を再利用しています。Liu 博士は次のように述べています。「モデルベースデザインと Simulink を利用すれば、新しいアプリケーションのために必要な変更を簡単に可視化できるため、変更の範囲と実装にかかる時間を最小限に抑えることが可能です」
- すべてのアプリケーション コードを自動生成. このコントローラーでは Embedded Coder を使って 10 万行を超えるアプリケーション コードが生成されました。Liu 博士は次のように述べています。「コードは自動生成されるため、矛盾がなく、維持管理も簡単でした。また、自動生成されるコードは、当社で義務付けられている MISRA C ガイドラインに準拠する、高品質なものであったということも重要な点です。手書きのコードでこのような一貫性と高品質を達成することは、非常に困難です」