日産、エンジン制御ソフトウェアの開発とテストを加速
「Simulink と Powertrain Blockset を使用して、動的なエンジン リファレンス モデルから開始し、複数のエンジンバリアントに応じた自動リサイズを行い、リサイズ結果のモデルをMIL と HIL の両方で再利用することが可能になり、作業期間が短縮され、エンジン制御ソフトウェア全体の品質を改善することができました」
課題
エンジン制御ソフトウェアの開発とテストを加速
ソリューション
Simulink と Powertrain Blockset によるエンジンモデルの構築、各エンジンバリアントに応じた自動リサイズ、およびMIL と HIL テストにおけるこれらの再利用
結果
- エンジンバリアントのモデル作成を数日から数時間に短縮
- コーディングコストを約 1/3 に削減
- HIL の準備期間を大幅に短縮
日産自動車株式会社(以下、「日産」)は、2022年までにニッサン インテリジェント モビリティを軸にした商品ラインナップの強化でコアモデル全ての刷新をし、20 以上の新型車の投入を行う計画です。この目標の達成のため、日産のエンジニアは MATLAB® と Simulink® のモデルベースデザインを使用して、エンジン制御ソフトウェアの開発および検証にかかる時間を削減しています。
日産は Simulink のシミュレーションを用いて、アプリケーション層にある全てSimulinkで記述されたソフトウェアコンポーネント (SW-C)をプラントモデルと組み合わせて評価しています。拡大する製品ラインにおける多数のエンジンバリアントに対応するため、日産のエンジニアは、Simulink および Powertrain Blockset™ を使用してエンジンモデルのバリアントを開発する標準化されたワークフローを確立し、モデルインザループ (MIL) テストとハードウェアインザループ (HIL) テストを実施しています。
日産のパワートレイン技術開発本部主管である加藤浩志氏は「Powertrain Blockset の動的エンジンモデルを出発点として用いることで、プラントモデルのバリアントを効率的に作成して調整することができました」と述べています。「MIL と HIL テストで同じモデルを使用できるため、必要となる労力を大幅に削減し、開発を加速することができました」
課題
日産のエンジン制御ソフトには、1500 近い SW-C が組み込まれています。日産のエンジニアは、排気量、気筒数、配置、最大トルクのバリエーションがある複数のエンジンについて、シミュレーションを用いてそれぞれの SW-C を評価しています。以前は、エンジンモデルのバリアントのパラメーターをエンジニアが手動で調整していました。そのモデルを使用したシミュレーションでは、計算負荷が大きく、シミュレーション時間が非現実的に長くなってしまいました。一方、単純なモデルは、高速でシミュレーションが行える反面、正確性が十分ではありませんでした。
MIL と HIL テストに異なるツールセットを使用していたため、日産のチームはリアルタイムの HIL テストを実施するために、全く新しいプラントモデルを作成する必要がありました。作業の重複をなくし、テストスケジュールを短縮するため、MIL と HIL テストの両方に同じプラントモデルを使用したいと考えていました。
ソリューション
日産は Simulink と Powertrain Blockset によるモデルベースデザインを用いて、パワートレインを制御するアプリケーション ソフトウェア (ASW) を開発し、テストしました。この ASW には、サプライヤーからの個別の SW-Cも一部含まれています。
日産のエンジニアは、エンジンプラントモデルのベースとして、Powertrain Blockset の SI Engine Dynamometer Reference Application を使います。 Resize Engine 機能と Recalibrate Controller 機能を使って、気筒数やエンジン排気量の設定に基づいて、エンジンモデルのリサイズとキャリブレーションパラメータの調整を自動で行います。必要に応じ (たとえば排気ガス再循環 (EGR) やターボチャージャーのサブシステムをモデル化する場合など)、エンジニアがモデルに追加の調整を加えます。
エンジンモデルの検証のために、前出の Reference Application に組み込まれたテストを実行し、シミュレーション結果のエンジントルクや他の性能指標を確認します。次に、検証済みのエンジンモデルをコントローラーモデル、トランスミッション モデル、および単純な車両モデルと組み合わせて、Simulink でシステムモデルを作成します。
エンジニアは、MATLAB で開発した自動テストのフレームワークを用いてMIL テストを実施し、コントローラーモデルが仕様を満たしているかどうかを確認します。このフレームワークは、テスト条件を設定し、シミュレーションを開始し、結果を可視化するためのグラフを作成します。
HIL テストの準備では、Simulink Coder™ を使ってエンジンモデルからコードを生成し、dSPACE® ハードウェアに展開します。リアルタイム HIL 環境でも、MIL で用いたものと同じテスト ケースを実行します。
日産は既にこのワークフローを量産車のエンジン制御ソフトウェアの評価に利用しており、今後の新型車での HIL や MIL テスト用のプラントモデルの開発にも利用する予定です。
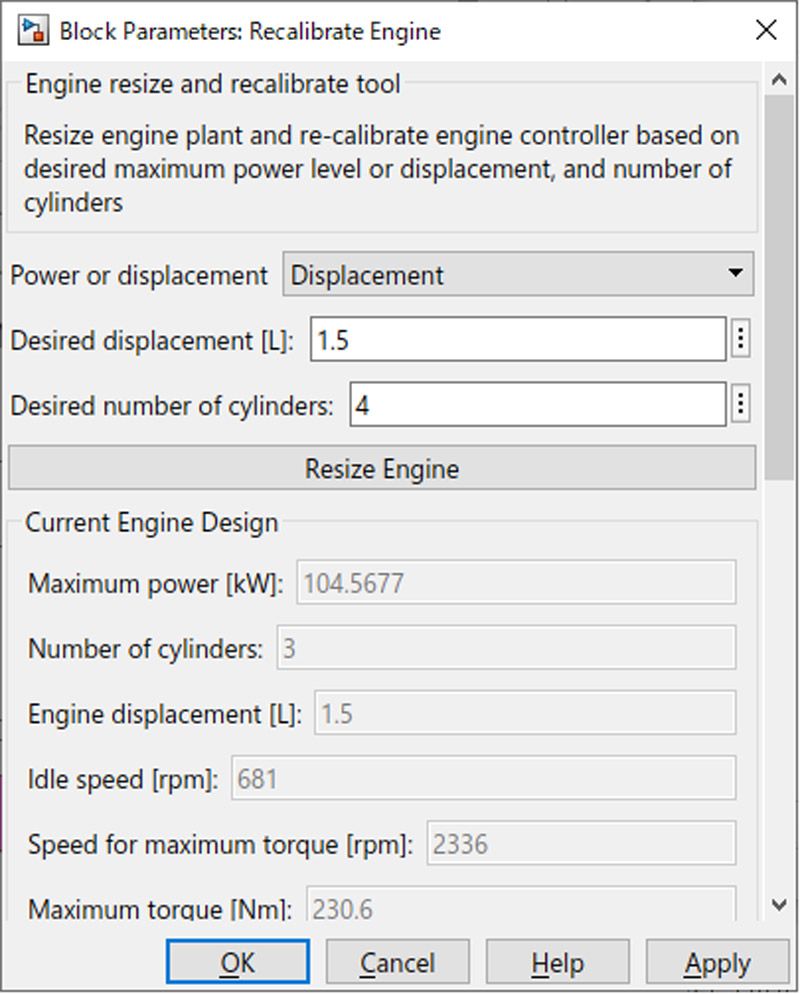
Resize Engine 機能のユーザーインターフェース
結果
- エンジンバリアントのモデルの作成時間を数日から数時間に短縮。「以前は、エンジンモデルを新しいエンジンバリアントに変更するために数日かかっていました。しかし現在では、Powertrain Blockset を用いることにより数時間で調整を行うことができます」と加藤氏は述べています。「結果として、品質を落とすことなく ASW の開発を加速することができました」
- コーディングコストを約 1/3 に削減。「Simulink で制御 ASW をモデル化し、モデルを実行可能な仕様として用いることで、OEM とサプライヤーの間で起こりうる誤解を解消しました」と加藤氏は述べています。「さらに、モデルからコードを生成することで、ハンドコーディングから起こるバグやヒューマンエラーをなくすことができました。このような改善によって、開発コストのうちコーディングに関しては約1/3に減少し、開発期間が短縮されました」
- HIL の準備期間を大幅に短縮。「Simulink と Powertrain Blockset を用いることで、MIL と HIL テストで同じモデルを使用することができます」と加藤氏は述べています。「両方の環境で共通のテストケース、プラントモデル、およびツールを使用できるので、HIL テストに必要なエンジニアリング時間を 1 週間から 1 日に短縮することができました」