STIWA によるオートメーション機器の総生産量の向上
「作業現場管理システム AMS ZPoint-CI は、大量の機械、プロセスおよび製品データを一日 24 時間収集しています。このデータを MATLAB および AMS Analysis-CI で即時に解析することで、精度が 10 倍向上し、総サイクル時間の 30% の削減、生産量の大幅な向上を達成しました。」
課題
高度な数学手法を適用して、オートメーション機器を最適化し、総生産量を向上
ソリューション
AMS ZPoint-CI を使用して、大量の生産データをほぼリアルタイムで収集し、MATLAB を使用してデータの解析および最適軌跡を特定
結果
- 総サイクル時間を 30% 削減
- 大規模なデータセットを数秒で解析
- 複数のマシンへの効率化された配布
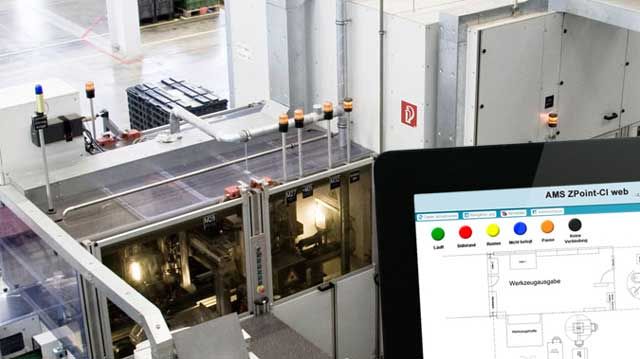
MATLAB をベースとする STIWA の作業現場管理システム、AMS ZPoint-CI および AMS Analysis-CI。© STIWA Group.
オーストリアの Attnang-Puchheim に本部がある STIWA Automation GmbH は、高パフォーマンス オートメーションにおける業界のリーダーです。4 つの拠点の 1200 名の従業員は、アセンブリ モジュールおよびプロセス モジュールに加えて自動化されたフィード システム、パッケージ システム、伝達システムを STIWA の顧客に提供します。
STIWA のエンジニアは MATLAB® を使用して、作業現場管理システム AMS ZPoint-CI によってほぼリアルタイムで収集された大量の生産データを解析します。このアプローチによって、時間最適軌跡を計算し、生産システムのサイクル時間を削減して、生産量を増加させることができます。
STIWA の製造ソフトウェアの最高営業責任者である Alexander Meisinger 氏は次のように述べています。「MATLAB および STIWA 製造ソフトウェアによって、機械システムの生産能力を最大化し、ソフトウェアのシステムの問題を診断および修正し、オートメーション機器を最適化するために収集したデータを迅速に解析するアルゴリズムを採用することができます。」
課題
典型的な STIWA システムは 8 秒ごとに、ノイズ、トルクおよびその他の機械測定値を保存する 150,000 のデータセットの、9 メガバイトを超える生の生産データを収集します。適切な許容誤差の特定、ロボットまたは柔軟な移送システム向けの時間最適追跡の計算または、たとえば、ベルトの張力の調整によるプロセスの変更のために、このデータはフィルター処理されてから処理されなければなりません。
これまで、STIWA のエンジニアは、PLC 用の IEC 61131-3 ストラクチャード テキストなどの低水準言語でデータ解析アルゴリズムを開発していました。このアプローチは工数を要するため、アルゴリズムが複雑になるにつれて機能しなくなりました。たとえば、軌跡計画アルゴリズムは、ジョイントの拘束がある 4 つの位置の軌跡を計算します。アルゴリズムに対する変更には、PLC コード実装に 1 日、エラーのデバッグにさらに 1 日必要です。
STIWA は、高度なアルゴリズムの開発と実行を高速化して大規模なデータセットから有益な情報を抽出し、エンジニアが低水準の実装の細部ではなく問題解決に集中するために、組み込みまれたデータ解析機能を備えた開発環境が必要でした。また大半の新任エンジニアにとってなじみのあるツールを使用することが必要でした。このツールによって、アルゴリズムを会社の既存の .NET 生産システムに統合することが容易になることが求められていました。STIWA は、利用可能なマルチコア ハードウェア インフラストラクチャにアクセスすることで、アルゴリズムの実行を高速化する必要がありました。
ソリューション
STIWA はデータ解析の実行と総生産量の最適化のために、MATLAB を使用してワークフローを実装しました。
このワークフローでは、STIWA のエンジニアは機械および製品データを MATLAB にインポートして、データのフィルター処理、リサンプリング、可視化を行い、問題および最適化の機会を特定します。
MATLAB で作業することで、エンジニアはデータ解析を自動化し、ロボット コンポーネントの時間最適軌跡を計画するアルゴリズムを開発します。アルゴリズムは Optimization Toolbox™ の関数を呼び出して、速度および空間の制限を含む定義された拘束に基づいて最適軌跡を計算します。
チームは Parallel Computing Toolbox™ を使用して、最大 6 つの処理コアを使用したワークステーションでの最適化を実行することで、軌跡の計算を高速化します。関数 fmincon
の暗黙的な並列化を使用して、アルゴリズムをベクトル化し、暗黙的な並列化のパフォーマンスを強化します。
コードを並列化する前に、エンジニアは MATLAB プロファイラーを使用してアルゴリズムを最適化し、最も時間がかかる関数を特定します。
単体テストの後で、チームは MATLAB Compiler™ および MATLAB Compiler SDK™ を使用して複雑なアルゴリズムを .NET コンポーネントとしてパッケージ化します。
.NET コンポーネントは、生産システムに実装される前にテストの最終段階を迎えます。
これらのコンポーネントを AMS ZPoint-CI および AMS Analysis-CI をベースとする STIWA の作業現場管理システムに統合することで、生産現場で閉じたコントロールを可能にします。.NET コンポーネントおよびこれらに含まれる MATLAB アルゴリズムは、約 10 秒ごとに呼び出され、収集されたデータの解析と機械パラメーターの調整が行われます。
結果
- 総サイクル時間を 30% 削減. 「MATLAB、Optimization Toolbox、AMS ZPoint-CI および AMS Analysis-CI を使用して時間最適軌跡計画を行うことで、機械プロセスの総サイクル時間を削減でき、生産量が大幅に向上することになります。」と Meisinger 氏は述べています。
- 大規模なデータセットを数秒で解析. 「効率的にするために、アルゴリズムは大量のデータをほぼリアルタイムで解析しなければなりません。」と STIWA のソフトウェア ツール開発エンジニアの Martin Werner 氏は述べています。「プロファイラー ツールを使用して MATLAB アルゴリズムを最適化し、Parallel Computing Toolbox を使用して複数のコアで軌跡最適化を実行することで、この高水準なパフォーマンスを達成しました。」
- 複数のマシンへの効率化された配布. STIWA のビジネス ユニット製造ソフトウェアの責任者である Michael Pauditz 氏は次のように述べています。「MATLAB Compiler SDK を使用して MATLAB アルゴリズムを .NET システムに統合することで、アルゴリズムを複数のマシンに容易に配布できます。」